Visión Comfacauca, publicación que resalta procesos innovadores de sus empresas afiliadas
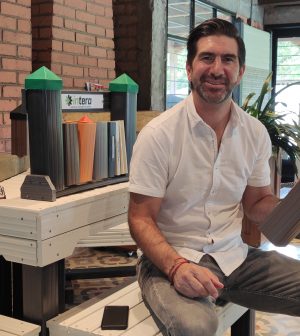
En la reciente edición virtual V.C. destaca emprendimientos de éxito como Intera, fabricante a partir de reciclaje; Beeler cervecera artesanal y el restaurante Entorno.
El periódico La Campana publica algunos de los interesantes reportajes que contiene la edición 24 de Visión Comfacauca, que se pueden apreciar en el sitio Web de la Caja de Compensación.
Intera protege el medio ambiente dándole nueva vida al plástico
Recién egresado en el 2006 de ingeniería industrial de la Fundación Universitaria de Popayán, (FUP), Andrés José Paz Arboleda, trabajó en el Instituto Tecnológico de Comfacauca, hoy Unicomfacauca, como vicerrector administrativo y financiero encargado, luego de un tiempo se quedó en la institución y ahí comenzó, no solo su historia profesional, sino su acercamiento al reciclaje como empresario.
Por esa época la Alcaldía, la Gobernación y universidades comenzaron a pensar en desarrollar un proyecto en el entonces relleno sanitario El Ojito, en Popayán, con unos equipos que reposaban en ese sitio desde hacía mucho tiempo.
Se metió en ese basurero a cielo abierto, en el que encontró a recicladores que separaban materiales de manera empírica, con los cuales producían suelas para zapatos, lo que le impactó, pues no lo habría imaginado.
Se empezó a darle estructura al proyecto, pero al final la Alcaldía, la Gobernación y las universidades no se pusieron de acuerdo. Paz Arboleda no se quedó quieto ante ese naufragio y tomó la iniciativa a título personal. Su primer acercamiento a la industria, fue una pequeña fábrica que producía objetos a partir del reciclaje de vidrio.
Esa empresa se acabó, pero no su deseo por la transformación de materiales de desecho, porque al tiempo en que los veía como materia prima, también pensaba en el aporte al medio ambiente y en generar empleo. Resolvió darle forma al proyecto abortado por la institucionalidad y la academia, con el reciclaje de plástico. Le tomó “cariño infinito”, como dice, al proceso de recolección. Por aquel tiempo no se pensaba en ese campo, nadie tenía idea de cómo transformar materiales, mucho menos cómo hacerlo y qué equipos utilizar.

negocio a futuro.
Comenzó a investigar sobre el reciclaje, cómo funcionaba, de qué forma, qué pasaba en Popayán al respecto, en Bogotá y en el mundo. Se dio cuenta de que Europa y Estados Unidos estaban muy enfocados hacia el reciclaje, pero en Colombia no. Se sabía que el reciclaje de metal y de papel estaba bien estructurado, pero el plástico no, que es el mayor contaminante en el planeta, en especial de los mares, los ríos y los bosques.
Su persistencia y testarudez lo han llevado a desarrollar ingeniería y tecnología del reciclaje
en una variedad de plástico, obviamente con errores y aciertos, pero creciendo en esta
industria. Montó la fábrica en Mosquera, Cundinamarca, y en el 2019 la trasladó a
Popayán. Con este industrial payanés dialogó Visión Comfacauca.
¿Cuál es el origen del proyecto Intera?
A.J.P.A. Averigüé que en Estados Unidos y en Europa había procesos de transformación
de plástico, más enfocados al material virgen, pero se empezaba la recolección y la
separación de los materiales. Ahí comienzo a darle forma y estructura al proyecto, enfocado
a un proceso de extrusión de plástico. Veía que en el Cauca los cerramientos de potreros y
corrales del ganado se hacían talando el bosque para suplir la necesidad de infraestructura,
a costa del agua por la deforestación que seca los nacederos. Entonces, con la ayuda de un
técnico, prendí esa vieja extrusora del Ojito, cero tecnologías, le puse un molde hechizo y
saqué un larguero de plástico. En el ITC solicité permiso no remunerado por un mes y
comencé a investigar. Di en Bogotá con una persona que conocía de equipos de extrusión.
Le dije de qué características requería el modelo, él me decía que no se lograba, fui terco y
lo logré.
¿Quién lo acompañó en ese proyecto?
A.J.P.A. En el 2009 me asocié con mi tío Carlos Felipe Chaux, y en octubre de ese año
contraté la fabricación de una máquina en Bogotá, la primiparada fue dura, hubo que
meterle más plata al equipo y luego de seis meses pusimos a andar la línea. Siempre he sido
apasionado por este tema, si no se hace con pasión no se logra nada. He sido operario de mi
propia línea de producción. Fueron seis meses de ensayo, prueba y error, gastando unos
recursos, hasta que se dio el primer producto, no lo podíamos creer. Lo puse en el mercado
en julio de 2010, año en que nos fue bien. En el 2011 tomamos la decisión de comprar
equipos con mejor tecnología, más eficientes, con capacidades diferentes, pensando en un
negocio a futuro.
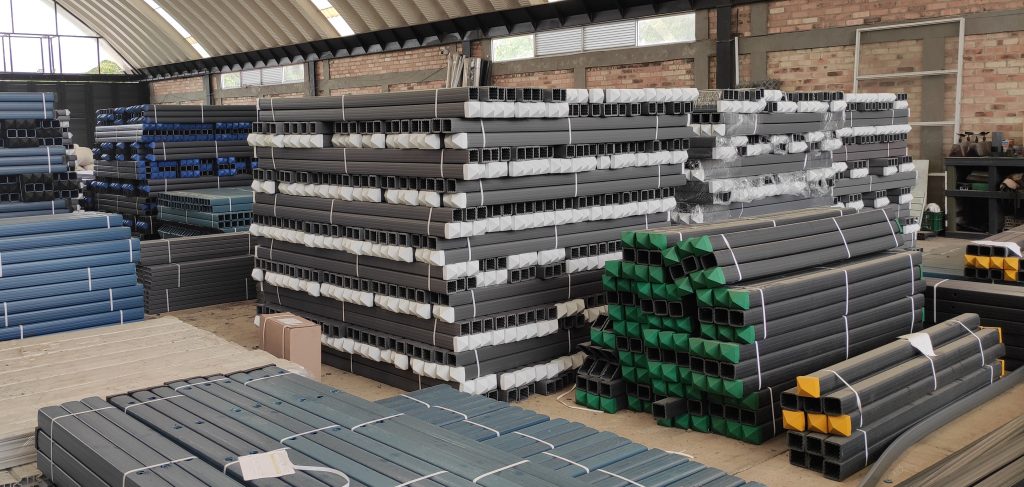
de flexión es mayor que otro material.
¿En dónde se estableció la fábrica?
A.J.P.A. En Mosquera, Cundinamarca, allí estuvo hasta el 2019. Dos años antes, en el
2017 se empezó el trabajo comercial, operativo. Echar a andar un negocio no es fácil, en
especial desde la tarea de recolección de los materiales, hacer un reciclaje organizado para
producir materia prima de calidad. Son 12 años de trabajo. Darle formalidad al reciclaje ha
sido un reto grande.
¿Qué hizo que regresara con la empresa a Popayán?
A.J.P.A. Vivía en el norte de Bogotá y la planta estaba en el municipio de Mosquera, eran
tres horas de ida y tres de regreso diarias, había días que eran hasta cinco horas en la
movilización. En 10 años se fue produciendo un desgaste. La calidad de vida en Bogotá,
depende de si el trabajo está cerca de la casa. Además, con mi socio vimos la posibilidad de
aportarle a Popayán, pues muchos de quienes han salido de la ciudad, creen que regresar es
devolverse en el tiempo, estancarse, yo lo veo diferente, porque además siento que aquí
están las oportunidades.
¿Qué pasó con la decisión del traslado a Popayán?
A.J.P.A. Me decían que me había enloquecido. Al principio me dio temor, sobre todo
porque tenía en el centro del país un mercado cautivo, especialmente en Bogotá,
Cundinamarca, Magdalena Medio, los Santanderes, etc. Alejarme mucho de mis clientes
era duro.
¿Evaluó los costos para regresar a Popayán?
A.J.P.A. Claro, se tiene que evaluar mucho eso. Hacer patrimonio empresarial en Colombia
es difícil. Si vemos la historia de las empresas en el país, que han hecho capitales y tienen
hoy empresas bien estructuradas, son de hace 50-60 -70 años porque en esas épocas había
más posibilidades, menos competencia. Hoy hacer patrimonio empresarial es muy
complejo, los costos no lo permiten, la carga impositiva es altísima, los bancos aprietan
fuerte. Obviamente, en Bogotá el costo fijo es más alto y hace que las empresas fracasen en
el intento. Esa fue también una de las razones por las cuales pensamos en el traslado.
¿Cuántos empleos estaba generando en Bogotá?
A.J.P.A. Quince empleos directos y más de 100 indirectos. En Popayán estamos generando
32 empleos directos y más de 100 personas alrededor del reciclaje, además de otros en
diferentes campos.
Acabando de llegar a Popayán, ¿Cómo le fue a Intera en paro, bloqueo, cuarentena y
pandemia?
A.J.P.A. Fue durísimo, todo el personal lo tenemos vinculado a la empresa. En el paro
fueron 47 días sin poder entrar a la planta, casi 80 días sin materia prima. Después vino la
cuarentena, con todo lo que implicó el encierro, los operarios permanecieron en la planta,
hospedados en una casa hecha con el material plástico que produce Intera. Con el apoyo de
los socios de la empresa se dispuso de toda la logística y recursos para que pudieran
permanecer en la planta, esa fue la forma de ponerla a andar. En la pandemia estuvimos
parados unos 23 días, más tiempo fue la parálisis provocada por el paro, que generó
muchos estragos tanto económicos como financieros.
¿Todo tipo de plástico sirve para la transformación industrial que hace Intera?
A.J.P.A. Hay siete clases de plásticos, la industria del PVC es diferente al Polietileno
Tereftalato, conocido como PET, en la planta solo utilizamos un polipropileno y un
polietileno de alta densidad. Capacitamos a los recicladores en la recolección, buscamos
mejorar su calidad de vida. Nos hemos aliado con asociaciones, especialmente con Armac,
con la que hemos estructurado un trabajo a futuro, pues pensar que Intera se puede
abastecer 100 % de Popayán, no es posible. Estamos haciendo en promedio una
transformación de 50 toneladas al mes, en Popayán jalonamos alrededor 10, 12 o 15
toneladas máximo, empezamos en ceros, la mayor parte viene de fuera.
¿Qué desechables aprovecha Intera?
A.J.P.A. Toda la línea de aseo del hogar, recipientes de límpido, Shampoo de ropa,
detergentes, tarros de aceite de carro, etc. Hay que a identificarlos y separarlos del resto del
reciclaje.
¿Qué productos está sacando Intera al mercado?
A.J.P.A. Tenemos tres líneas de productos. Estamos enfocados en soluciones de
cerramiento para vivienda rural y urbana, delimitación de potreros, lotes, etc. El plástico en
estos casos es como la madera. Con los perfiles que fabricamos se hacen mesas, bancas,
sillas, materas, pisos, mobiliarios urbanos, aulas, bodegas, etc. El plástico como materia
prima es el material de mayor durabilidad y asepsia, su capacidad de flexión es mayor que
cualquiera otra, la resistencia y la rigidez son excelentes. Los perfiles se trabajan por
colores y personalizados.
You must be logged in to post a comment Login